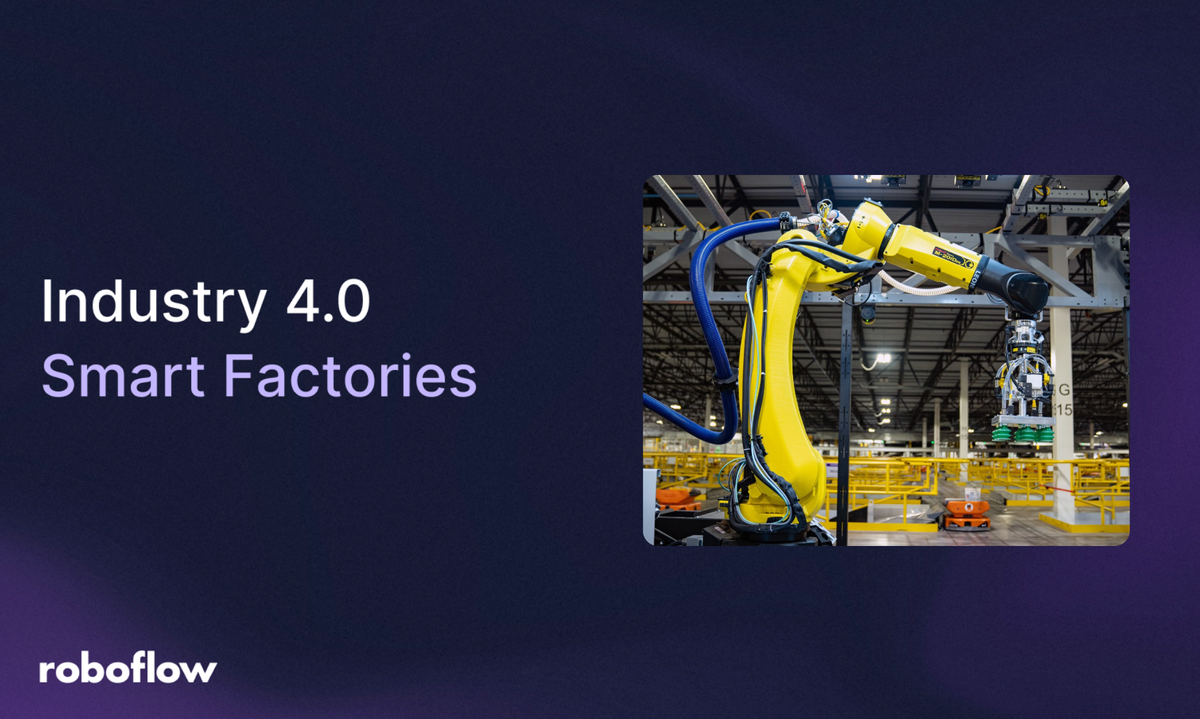
Imagine a factory floor where machines think, see, and communicate. What you’re picturing is Industry 4.0 - and it’s arrived. It’s the newest phase of manufacturing, moving beyond automation into intelligent, data-driven operations.
Industry 3.0, emerging in the 1970s, marked the rise of automation through the integration of Programmable Logic Controllers and computers in manufacturing. This era saw the mass adoption of robotics, Computer-Aided Manufacturing software, and the incorporation of electronics into industrial machines such as CNC machines and lathes. Information technology became a crucial part of production, enabling greater precision, efficiency, and scalability in manufacturing processes.
Industry 4.0 is about integrating AI, Internet of Things (IoT), computer vision, robotics, and cloud computing to create facilities that are more efficient, adaptive, and scalable than ever before.
Today, advancements in deep learning and machine vision - fueled by increased computational power, vast datasets, and improved neural networks - have made AI-driven manufacturing more accessible and practical than ever. These technologies allow deep learning models to continuously learn and adapt to new data, enabling rapid deployment and remote optimization.
Furthermore, manufacturing engineers now have unprecedented access to real-time data, making it easier to audit, analyze, and optimize performance at every stage of production.
Exploring Industry 4.0
Industry 4.0 is a shift in manufacturing, powered by automation, AI, and connected systems, that’s transforming how factories operate. If Industry 3.0 was about adding computers to machines, industry 4.0 is about making those machines intelligent.
The foundation of Industry 4.0 is the ability to connect machines, sensors, and systems through IoT and process vast amounts of data in the cloud. IoT enabled cloud computing now facilitates scalable, real-time data analysis, allowing manufacturers to monitor performance, predict failures, and optimize production.
Furthermore, the rise of connected, automated production environments has enabled “lights-out” manufacturing, where smart factories operate with minimal human intervention. Predictive maintenance powered by AI and IoT ensures equipment uptime, while improved demand planning through real-time data analytics helps manufacturers optimize inventory and reduce waste.
Robotics has become more capable and widespread, with autonomous mobile robots (AMRs) and robot arm systems playing a larger role in manufacturing.
And, once limited to prototyping, additive manufacturing has now reached large-scale adoption, particularly with metal 3D printing. Industries such as aerospace have pioneered this shift. For example, GE’s 2015 introduction of a 3D-printed jet engine part consolidated 19 components into a single structure, reducing weight and complexity.
To summarize the result of all these advancements, instead of just automating tasks, systems are now capable of learning, predicting, and optimizing on their own. Sensors, IoT devices, and AI-driven analytics collect real-time data from production lines, helping to reduce downtime, catch defects early, and streamline operations - without human intervention at every step.
Previously, quality control meant random sampling or relying on human inspectors. However, as just one example, an electronic board can contain around 5,000 to 8,000 solder joints, making it nearly impossible for humans to inspect each one accurately with the naked eye.
While during Industry 3.0 it was possible - with traditional machine vision models - to detect more binary details such as weld present vs. not present, Industry 4.0 allows a model built to determine a good vs. bad weld. With AI-powered vision systems, every product on your line is analyzed in milliseconds, and defects are spotted with greater accuracy than by the human eye.
How does this work? PCB inspection cameras would capture high-quality images of the circuit board. Computer vision algorithms would then extract specific information, such as joints, corners, and textures. And the extracted information could then be processed and analyzed to detect defects or misplaced joints. A visual inspector would review the defects spotted by AI and make any necessary adjustments.
And it's not just quality control. Industry 4.0 is reshaping predictive maintenance, supply chain logistics, and even worker safety. For example, Nestlé Purina is reaping the benefits of advanced robotics and AI-driven software infrastructure. The company has deployed a Boston Dynamics Spot robot that conducts regular inspections of their facility, monitoring for air leaks and conducting thermal checks on motors, bell housings, and gearboxes.
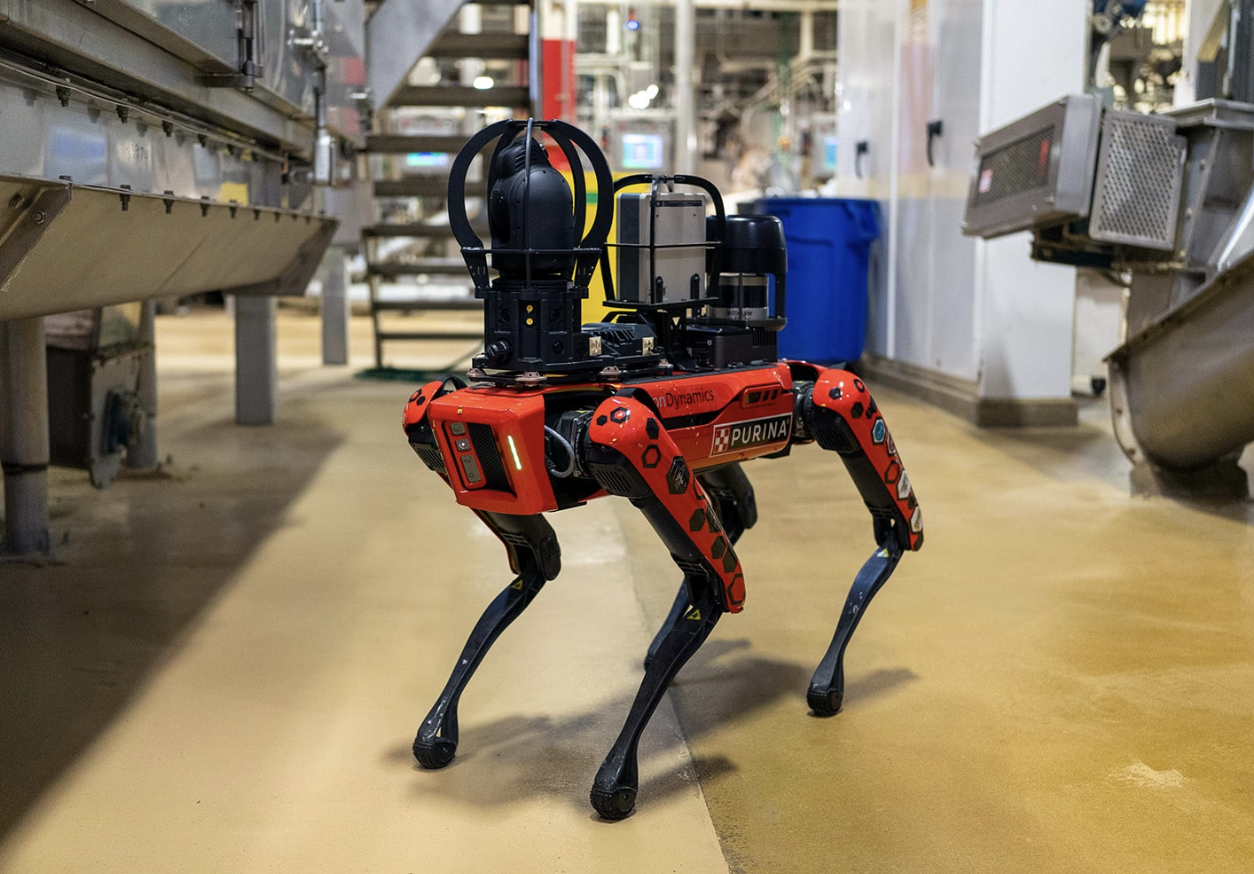
Discover Popular Industry 4.0 Technologies
As enterprises embrace this transformation, they’re leveraging a variety of advanced tools and systems to enhance efficiency, agility, and productivity. Let’s explore some of the most popular and impactful Industry 4.0 technologies transforming manufacturing.
1. Big Data and Analytics
The foundation of Industry 4.0 lies in the vast amounts of data generated by connected devices and systems. This data presents an opportunity to uncover actionable insights that drive efficiency, predict demand, and optimize operations—from supply chain logistics to resource allocation.
The rise of data analytics in the 2000s has transformed how businesses leverage information, enabling more informed decision-making than ever before. As we continue to measure more, we can do more with that data, refining processes and improving outcomes. Looking ahead, large language models (LLMs) will further enhance data analysis, making it easier to extract valuable insights and drive smarter automation across industries.
2. Machine Vision
Computer vision is reshaping how factories approach quality control and monitoring through edge AI. With AI-powered cameras and sensors, machines can detect defects, track products in real-time, and even predict potential issues on the assembly line. Vision AI can be thought of as a highly-efficient "eyes" system that continuously inspects products while speeding up the process.
3. Internet of Things (IoT)
The backbone of Industry 4.0 is IoT - essentially, everything gets connected. Machines, sensors, and devices talk to each other in real-time, gathering and exchanging data. The machines can tell you when they're working properly, when they need maintenance, or when they're underperforming.
4. Artificial Intelligence (AI) and Machine Learning
At the heart of AI in manufacturing is the ability to make intelligent decisions from data. AI can help optimize production lines, predict maintenance issues, and even drive robotic systems. The beauty of AI is that it doesn’t just collect data - it learns from it, constantly improving operations.
5. Robotics and Automation
Robotics has evolved from simple programmed machines into essential team members in Industry 4.0 factories. Robots such as AMRs, Cobots, and AI virtual training are relatively new. In addition, low cost robots from China are also changing the industry.
While industrial robots have been used since the 1970s, their capabilities have grown dramatically over the decades. Early developments, such as Victor Scheinman’s Stanford Arm in 1974 and the rise of manufacturers like FANUC and KUKA, laid the foundation for automation in manufacturing. By the 1980s, robots were widely adopted in the automotive industry for tasks like welding and painting.
The 1990s saw advancements in sensors and software, enabling robots to take on more complex roles and work alongside human operators. In the 2000s, collaborative robots emerged, designed to safely interact with workers. The 2010s brought AI and machine learning into robotics, allowing machines to handle adaptive tasks, while the 2020s have ushered in the widespread use of Autonomous Mobile Robots, robotic picking systems, and AI-driven solutions in warehouses and manufacturing lines.
6. Cyber-Physical Systems
CPS are systems that integrate the physical world with the digital world. Essentially, these are highly connected sensors, processors, and actuators that are tightly integrated with physical processes, allowing for real-time interaction and control.
In the future we may see augmented reality and virtual reality making an impact as well. For example, AR can project step-by-step assembly instructions directly onto a worker’s field of view, reducing errors and speeding up production processes. And engineers can use VR to simulate a factory floor, experiment with layout changes, or test new machinery before implementation.
4th Industrial Revolution and Smart Factories
86% of surveyed manufacturing executives believe smart factory solutions will be the primary driver of competitiveness in the next five years, according to a 2024 Deloitte report. This underscores the industry's growing investment in connected workforce solutions, real-time data insights, and automation to maintain an edge. In fact, 94% of industry executives cite digital transformation as a top strategic priority.
However, a critical challenge remains: the ongoing exodus of manufacturing talent to the tech sector, where higher salaries and better working conditions attract skilled engineers. Despite this, companies such as Tesla, SpaceX, Anduril, and Rivian are leading the way in domestic smart manufacturing, while Apple also maintains a U.S.-based production footprint.
As manufacturers navigate the complexities of Industry 4.0, the focus for building smart factories extends beyond efficiency and competitiveness to broader transformation initiatives. Companies are not only embracing digital technologies to enhance productivity, but are also leveraging them to drive sustainability, workforce evolution, and new operational models.
Smart factories are driving more sustainability and energy efficiency
The integration of advanced technologies helps manufacturers minimize waste, reduce energy consumption, and lower their environmental impact. Xiaomi's “Dark Factory" in Changping, China, is a cutting-edge example of Industry 4.0 in action, redefining efficiency and automation in manufacturing. Xiaomi Founder and CEO Lei Jun said the dark factory has 11 production lines and 100 percent of key processes are automated.
Operating with minimal human intervention, this fully automated facility relies on advanced robotics, artificial intelligence, and IoT-enabled systems to streamline smartphone production - producing new foldable phones at a rate of one device every three seconds around-the-clock. The factory runs 24/7 in a "lights-out" environment, significantly reducing energy consumption and operational costs while maximizing precision and output.
As another example, at EcoStruxure, Schneider Electric is implementing the Internet of Things (IIoT) throughout their global supply chain. Across their Smart Factories and Smart Distribution Centers, they’ve reduced energy costs by between 10% and 30% and maintenance costs between 30% and 50%.
The rise of Industry 4.0 technologies has also reshaped the workforce in manufacturing
With the exodus of capable engineers as well as new technology, enterprises are focused on upskilling and reskilling their workers. For example, Bosch has created training programs for its workers to enhance their technical skills: More than 130,000 participants acquired knowledge in technologies of the future such as electromobility, software engineering, and Industry 4.0.
In addition, roles are evolving. There is growing demand for data scientists, analysts, and engineers who can interpret and leverage this new data. At GE Aviation, technicians have evolved into “digital workers” who leverage augmented reality (AR) and AI-powered tools to improve efficiency in aircraft engine maintenance. Smart glasses provide assembly information hands-free, putting instructions right in front of workers’ eyes. The technicians also use wearable devices to access real-time data and interact with 3D models.
Industry 4.0 Manufacturing Examples
To see what Industry 4.0 looks like in practice, let’s look at how real companies are using AI, automation, and connected systems to transform their operations. One of the biggest goals of industry 4.0 was lights out manufacturing and lights out warehouses. Japan was an early leader with FANUC's Japanese factories in 2001, and China has been in the news recently for implementing fully “lights-out” factories. Xiaomi’s “lights-out” factory operates round-the-clock with zero humans employed.
BMW is using computer vision to inspect vehicles during production. Instead of relying on human inspectors or random sampling, cameras powered by deep learning scan every single car for defects such as scratches, misaligned parts, even microscopic paint imperfections.
In express logistics, AI-powered sorting robots are increasing sorting capacity by some 40% or more. For example, Amazon’s Robin, one of the most complex stationary robot arm systems Amazon has ever built, is an AI-powered robotic arm designed to identify, pick, and sort packages with high speed and accuracy. Using computer vision, deep learning, and advanced sensors, Robin can recognize package labels, determine the best way to grip each item, and seamlessly direct it to the correct chute for delivery.
The Future of the Smart Factory and Manufacturing 4.0
While Industry 4.0 promises great benefits, a solid strategy and effective execution is necessary to succeed. According to Automation, a successful digital transformation strategy aligns with the company’s core business goals and focuses on five key pillars:
- People: Up-skilling the workforce to adapt to new technologies.
- Process: Streamlining operations through automation and optimization.
- Technology: Implementing cutting-edge tools like AI, IoT, and robotics.
- Data: Leveraging real-time data to make informed decisions.
- Ecosystem of Partners: Building an integrated network of technology partners.
Your strategy should also focus on key drivers such as competitive advantage, agility, sustainability, and customer-centric innovation.
As manufacturers continue to adopt Industry 4.0 technologies, it’s best to pursue a comprehensive strategy that balances innovation with execution. Companies that integrate smart technologies like robotics, AI, IoT, and 5G while aligning their efforts with business objectives will be best positioned to navigate the challenges and opportunities of the Fourth Industrial Revolution. The future of manufacturing is digital, and those who embrace this transformation will unlock new levels of productivity, agility, and sustainability.
Ready to learn how vision AI could benefit your factory this quarter? Roboflow is free to get started and easy to scale up. We’re SOC 2 Type II compliant, support custom security rules, and power customers operating at global scale with terabytes of data today. Talk to an AI expert to discuss your unique manufacturing use cases.
Cite this Post
Use the following entry to cite this post in your research:
Trevor Lynn. (Mar 20, 2025). What Is Industry 4.0? Smart Factories and The Fourth Industrial Revolution. Roboflow Blog: https://blog.roboflow.com/industry-4-0/