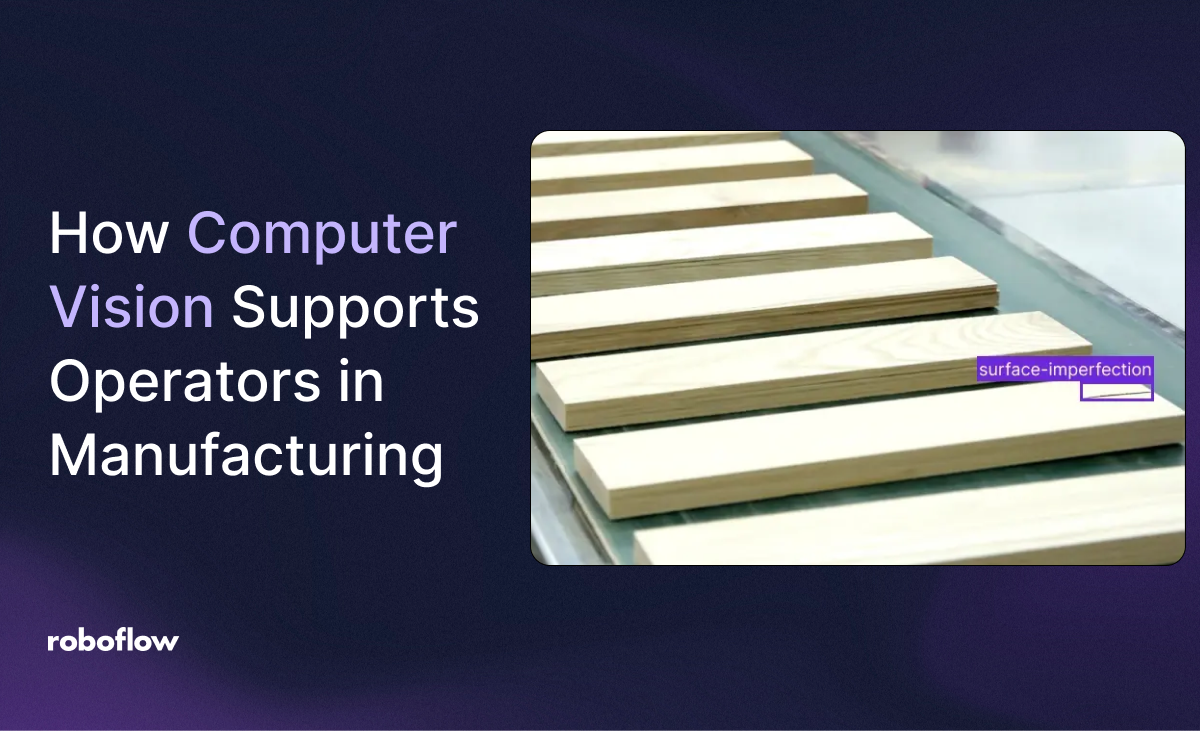
Operators are at the center of value creation on the floor. They build, inspect, and make real-time decisions that keep production running and products within spec. Their process knowledge and adaptability are critical to maintaining output, quality, and flow.
Roboflow builds on that foundation. Our computer vision platform brings consistent, high-speed visual inspection directly to the station. Using Roboflow, you can identify defects, confirm assembly details, and surface actionable insights that would be hard to catch with the human eye alone, especially at scale.
With Workflows, you can create manufacturing vision applications in your web browser and empower your engineers with what they need to deploy them to tens or even hundreds of cameras across multiple facilities.
Computer vision isn’t about removing people from the process. It’s about extending the capabilities of skilled operators. Vision AI reduces repetitive inspection tasks and adds a layer of real-time feedback that helps operators focus on what matters most: keeping quality high, minimizing downtime, and driving continuous improvement.
How computer vision reduces inspection load
Operators are often responsible for detecting visual defects, confirming part orientation, verifying markings, or checking for assembly completeness, all while staying within takt time. These tasks require focus and repetition, which can lead to fatigue and variability over time.
AI reduces this load by handling routine visual checks. For example, instead of manually confirming the presence of a label or the correct orientation of a part, a vision model can verify it automatically. This frees up the operator to monitor process flow, respond to equipment issues, and focus on safety or quality-critical tasks.
When the repetitive checks are handled automatically, the operator can concentrate on decision-making and continuous improvement. It's about shifting the operator’s time toward higher-value activities without removing their oversight.
Consistent quality across shifts and teams
The quality of visual inspection can vary depending on who is performing the task and when. Fatigue, lighting conditions, and differences in experience can all impact results. AI provides consistency by applying the same standards to every part, every time.
Once an inspection system is built, it follows the same visual criteria across all shifts. It doesn't get tired, and it doesn't guess. This helps reduce variation between operators and builds trust in the inspection process, while empowering operators to intervene when required rather than manually inspecting everything.
In addition, inspection results are recorded automatically. This creates a reliable log of pass/fail outcomes that supports traceability and continuous improvement. It also helps new team members ramp up faster, since the system supports consistent training and feedback.
Inline error detection that supports lean goals
In lean manufacturing, the goal is to detect problems where they happen and stop defects from moving downstream. If a fastener is missing or a part is out of alignment, it's better to catch that at the workstation than at final inspection.
With AI, issues are caught in real time. Vision models can check for part presence, alignment, orientation, labels, and surface defects as part of the standard process. When something is off, the system alerts the operator so it can be fixed immediately.
This approach supports lean principles like quality at the source and error-proofing. It also helps keep lines flowing without introducing additional inspection bottlenecks.
Real-time feedback for better decision-making
When defects are discovered late in the process, it often leads to rework, scrap, or missed delivery targets. AI provides immediate, station-level feedback so problems can be corrected before more parts are affected.
If a part is missing a component or something doesn't meet spec, your system can flag it right away. This allows the operator to respond quickly and prevent further defects from moving down the line.
Real-time alerts also help teams spot trends faster. If a pattern is forming, like a tool drifting out of tolerance or a batch of materials showing cosmetic flaws, the data is there to back it up. Operators and team leads can use this information to act early and avoid costly downtime or escapes.
AI that fits into the operator workflow
Roboflow is built to work alongside operators, not around them. It integrates into existing workflows and tools without adding complexity or slowing down production. Whether running in the background, displaying visual feedback on a monitor, or connecting to an HMI or MES system, the technology supports how operators already work.
Operators should be involved in defining what’s being inspected and how. Their process knowledge is critical to making sure the vision system is focused on the right tasks. When operators are part of the setup and feedback loop, they’re more likely to trust the tool and use it effectively.
This isn't just about detecting defects. It's about building confidence, improving workflow, and giving operators better visibility into their process.
Computer vision: an advanced assistant for operators
Computer vision gives operators better tools to do what they already do best, build, inspect, and maintain product quality. It doesn't take their job away. It helps remove the repetitive tasks that slow them down or introduce variation.
By automating standard checks, improving consistency, and delivering real-time feedback, vision supports stronger outcomes on the floor. And when operators are supported with tools that work the way they do, the entire operation benefits, from fewer defects to faster cycles and better process control.
This is what it means to empower the people who make manufacturing work.
Interested in bringing computer vision to your factory floor? Contact our enterprise sales team to learn how to get started.
Cite this Post
Use the following entry to cite this post in your research:
Jack Obert. (Apr 17, 2025). How Computer Vision Supports Operators in Modern Manufacturing. Roboflow Blog: https://blog.roboflow.com/computer-vision-manufacturing-operators/