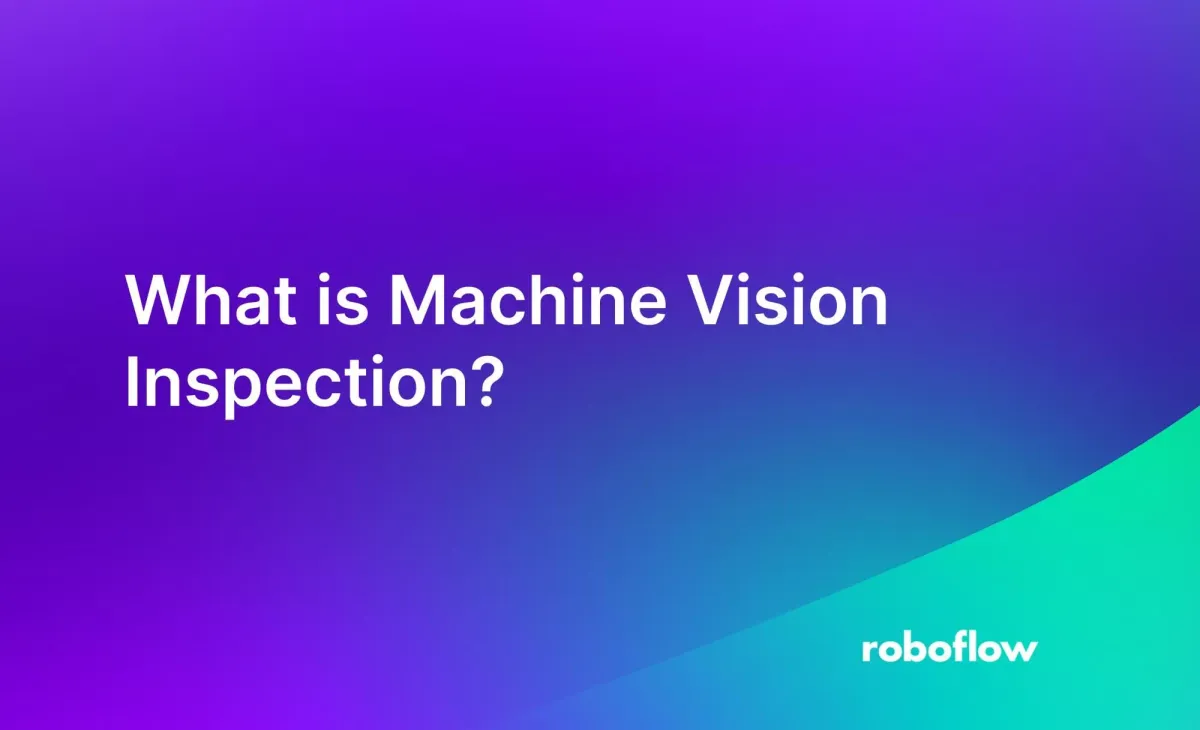
You can use machine vision, also referred to as computer vision, to inspect products. With a machine vision model, you can identify the presence or absence of parts in an object on a conveyor belt, information that you can use to inform if a part is correctly assembled. You can search for anomalies, such as the presence of cracks, dents, and stains.
In this guide, we are going to discuss what machine vision inspection is and use cases for this technology in manufacturing. We will also discuss how custom trained computer vision models can be used to accurately identify features in a product.
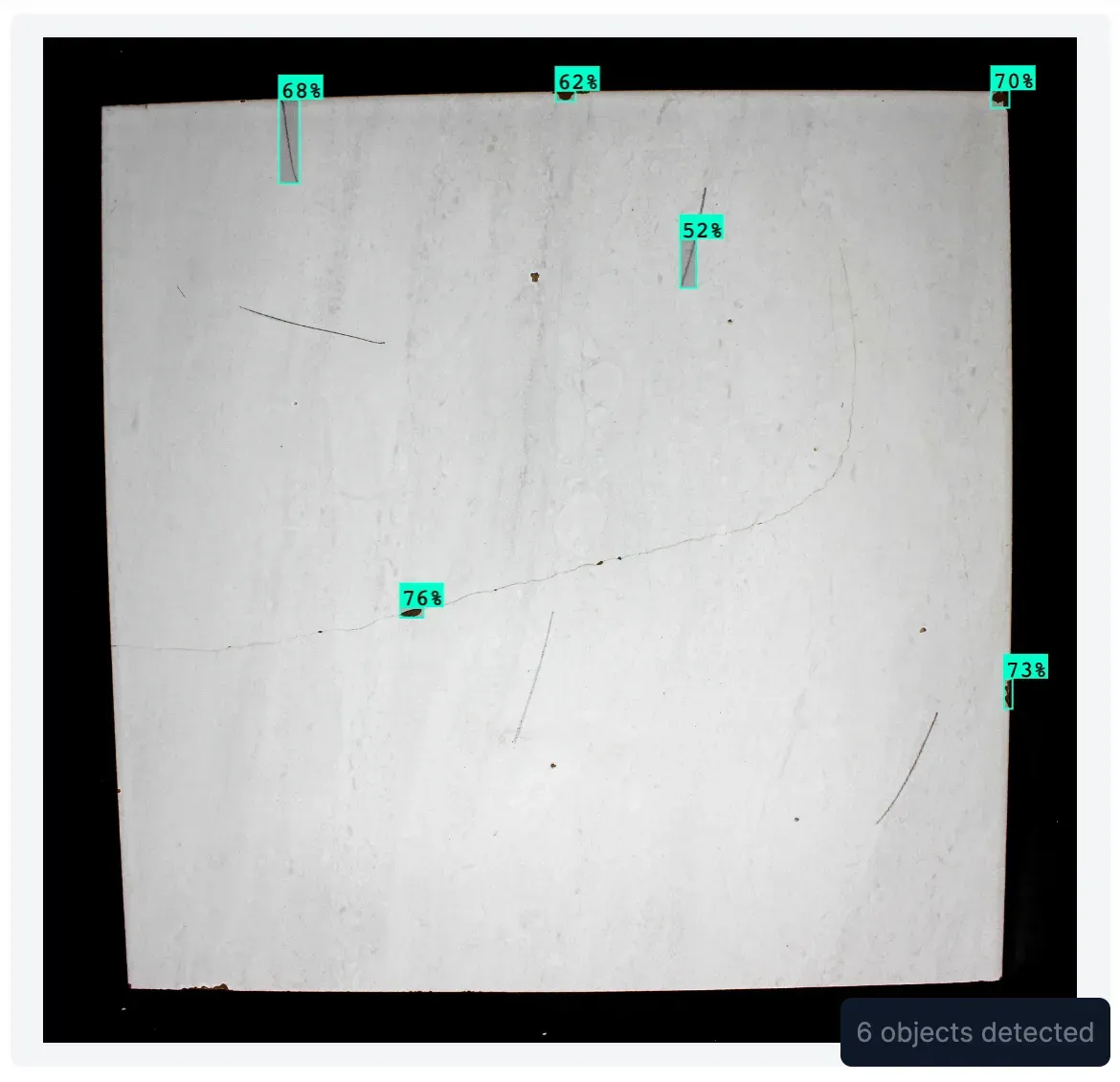
What Is Machine Vision Inspection?
Machine vision inspection refers to validating the quality of a product. A machine vision inspection system may check for the presence of all of the required parts on a component, or whether a defect is present on a product, among other quality checks.
There are two main fields of techniques used in machine vision inspection:
- Traditional machine vision, which uses tools like edge detection, color analysis, and pattern recognition to identify properties in a product, and;
- Deep learning-based computer vision, which uses neural networks to identify or classify objects.
With deep learning techniques, you can train a model to identify exact properties in an image. For example, you can train a milk bottle detection model to identify bottles and bottle caps. Then, you can write logic that records unexpected behavior, such as when there is no cap in the region of a bottle after the capping process has completed.
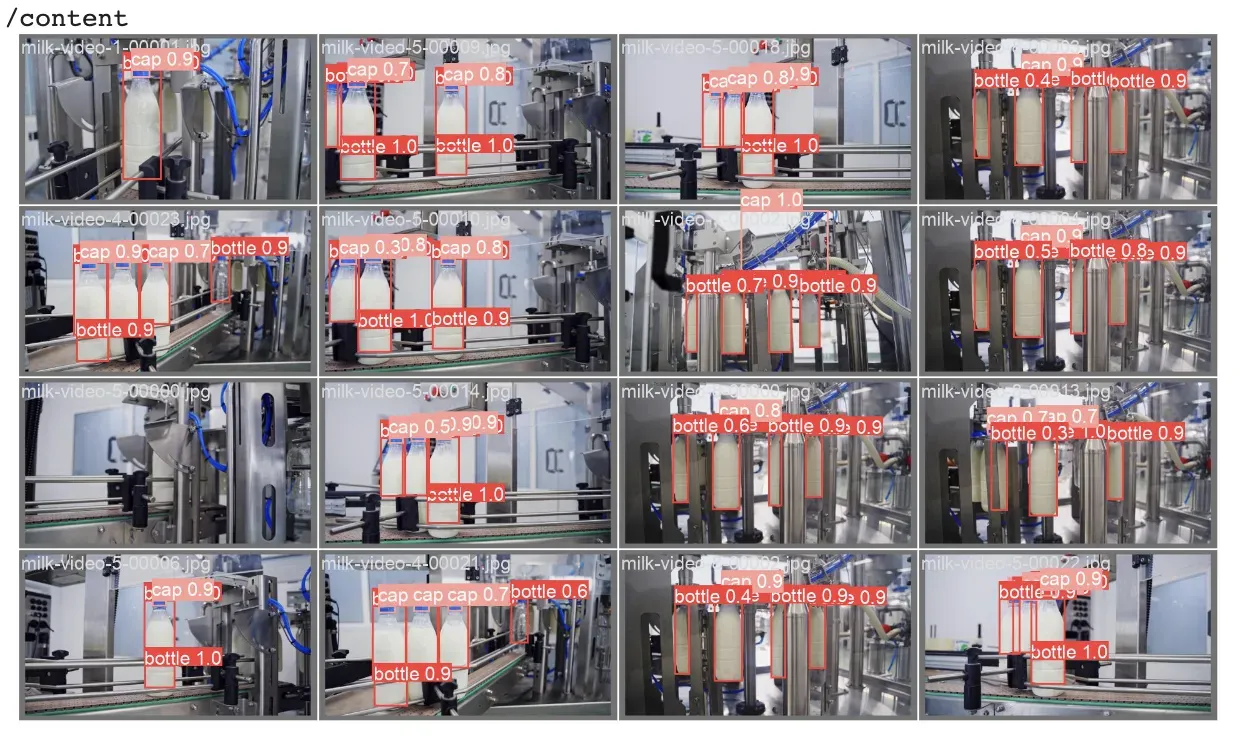
Deep learning techniques involve gathering images representative of your use case then training a model to identify or classify objects of interest.
Advancements in computer vision models has made this technique common practice in manufacturing because it is flexible, customizable, and user friendly. Deep learning models can be trained with a few hundred images and run on devices like a Raspberry Pi or NVIDIA Jetson.
This means in just a few hours, engineers can update models to accommodate for changes in the manufacturing process and have them running at the edge in real-time. Traditional machine vision is rules-based and difficult to adjust which means investments in cameras or systems can quickly become obsolete.
You can use a computer vision platform such as Roboflow to build a deep learning-based machine vision inspection system. Roboflow provides the utilities you need to gather images, annotate objects of interest, and train a model. You can then deploy your model to the edge using edge deployment devices like an NVIDIA Jetson, or by processing video in your factory over a protocol like RTSP.
Use Cases for Machine Vision Inspection
There are a myriad of use cases for machine vision inspection, including validation of:
- The presence or absence of objects (i.e. that there are objects on the conveyor belt).
- If an object is the right color (i.e. the color of a t-shirt).
- A part contains all the necessary sub-parts (i.e. that a bottle has a cap).
- The number of items in a region (i.e. the number of pills going into a bottle).
- Identifying the presence of mandatory labels (i.e. sell-by dates).
Machine vision can be deployed with any camera, no matter how small the object. If an object or defect is identifiable to the human eye, you can train a computer vision model to identify the object and instances of defects.
Deep Learning in Machine Vision Inspection
There are four main categories of computer vision models that can be used for automated inspection:
- Object detection, which involves identifying the general location of objects of interest.
- Classification, which assigns an image one or more labels depending on its contents.
- Segmentation, which identifies, at the pixel level, objects in an image.
- Keypoint detection, which allows you to identify specific points in an object and how they relate to each other.
The type of model you use for vision inspection depends on the use case you are trying to solve. For example, consider a scenario where you are identifying whether ice cream has melted on a manufacturing pipeline. You could use object detection to identify two classes: a whole ice cream and an ice cream that has partially melted.
On the other hand, suppose you need to check that an object is correctly aligned on a conveyor belt. You could use a keypoint detection model to check the orientation of the object is correct. For example, you could use keypoint detection to flag if an ice cream was at an angle on the conveyor belt, a scenario that could cause problems downstream when the food needs to be packaged.
Machine Vision Inspection Conclusion
Machine vision inspection is an essential part of quality assurance in modern manufacturing facilities. Over the last few years, there has been significant investment in deep learning technologies which are now being deployed in manufacturing facilities around the world. For example, object detection is used to identify defects on wood; segmentation is used to accurately identify regions for use in analyzing the color of part of a product. Learn more about how machine vision works in manufacturing.
Using a computer vision platform like Roboflow, you can build custom solutions for use in identifying defects and inspecting products. Roboflow provides all the tools you need to build a custom solution, from secure data collection and labeling tools to model training and edge deployment solutions.
Over 15,000 organizations around the world use Roboflow technology to solve business problems, from identifying product defects on assembly lines to identifying potential safety issues in critical infrastructure.
Learn more about using Roboflow for machine vision inspection by speaking with an AI expert.
Cite this Post
Use the following entry to cite this post in your research:
James Gallagher. (Jan 10, 2024). What Is Machine Vision Inspection?. Roboflow Blog: https://blog.roboflow.com/what-is-machine-vision-inspection/