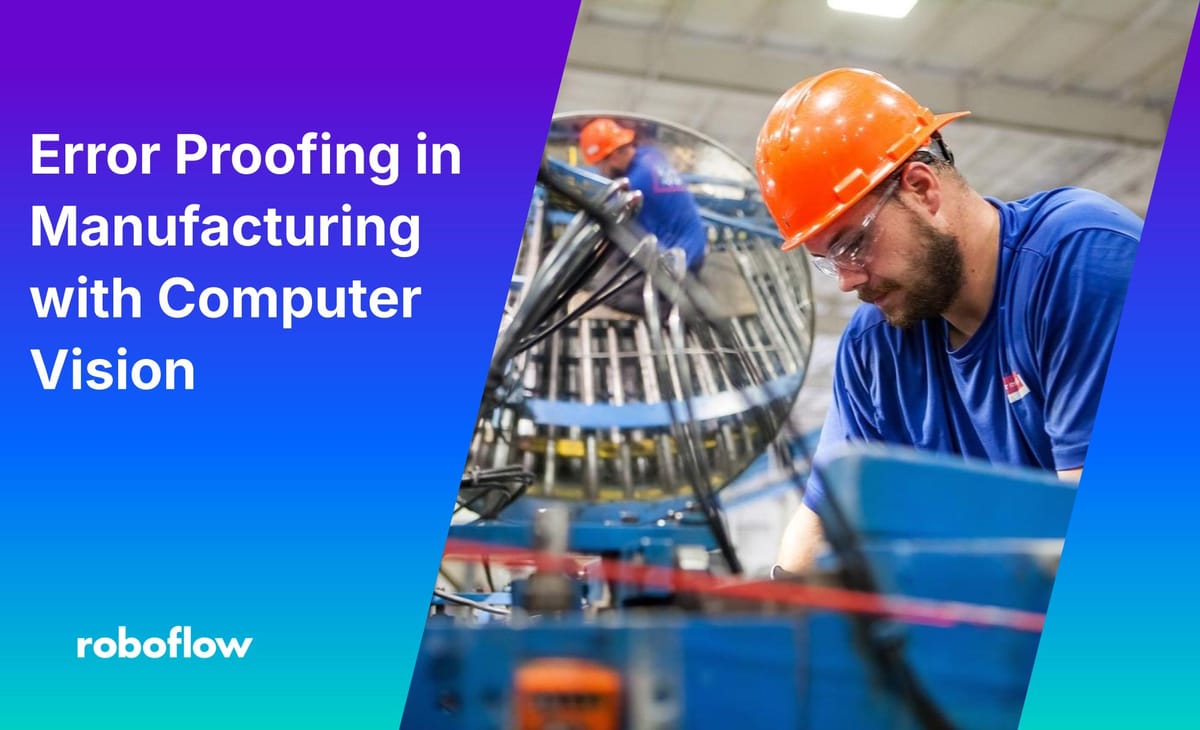
Mistakes during manufacturing can potentially eat up 20% of a company's revenue. Error-proofing, also known as poka-yoke, is a strategy used in manufacturing to prevent mistakes and make sure that products are made correctly. By creating processes that reduce or eliminate errors, manufacturers can cut down on waste, improve the quality of their products, and work more efficiently. While traditional methods like mechanical guides and sensors have helped reduce errors, they have limitations.
Manufacturers can use computer vision to catch defects more accurately and efficiently. Computer vision can help lower costs, improve product quality, and increase operational efficiency.
In this article, we'll explore exactly how error-proofing AI is used in manufacturing. Find out how over half the Fortune 100 is quietly winning with vision AI. Let’s get started!
The Importance of Error Proofing AI in Manufacturing
Errors in the manufacturing process can lead to serious problems, like wasted materials, higher costs, and unhappy customers. Error-proofing techniques are designed to catch and prevent these mistakes before they become bigger issues. They reinforce processes so that operations can run smoothly and products can meet high standards.
When errors happen, they often require rework. Manufacturers need to go back and fix the problem to ensure the final product meets the required quality standards. Rework can be both expensive and time-consuming. In fact, if a defect is found later in the production process, it’s likely much more costly to fix than if it had been caught earlier. That’s why effective error-proofing is so important. By identifying errors early, companies can avoid costly fixes, reduce waste, and make their processes more efficient.
How Computer Vision Enhances Error Proofing
Computer vision is redefining error-proofing in manufacturing by detecting defects in real time on production lines. These systems are designed to use computer vision techniques like object detection and instance segmentation to spot issues like scratches, misalignments, and assembly errors as products move along the line. Unlike manual inspections, which can vary in accuracy and are prone to human error, computer vision systems can work nonstop with incredible precision.
These systems are configured to capture high-resolution images or video streams of products on the assembly line. Using models trained on vast datasets of product images, the computer vision system can differentiate between normal and defective items with a high degree of accuracy. Automating error-proofing using computer vision also speeds up production and reduces the risk of defects causing recalls or customer dissatisfaction.
Types of Defects Detected by Computer Vision
Computer vision systems can identify various types of defects during the manufacturing process. This comes in handy because just one manufacturing process can result in many different defects. For example, a single production line might produce surface scratches, dimensional inaccuracies, or assembly misalignments.
Here are some of the common types of defect detection that can be done with computer vision:
- Surface Defects: Issues like scratches, dents, cracks, or stains can appear on a product's surface. These surface defects can compromise the final product's appearance and functionality.
- Dimensional Inaccuracies: Issues can arise when a product’s size or shape fails to match the specified dimensions. Such dimensional inaccuracies can lead to fit and function issues, especially in products that require precise measurements.
- Misalignments: When components are not properly aligned during assembly, misalignments occur. These defects can cause operational failures or weaken the overall integrity of the product.
- Color and Pattern Defects: Variations in color or patterns may develop due to manufacturing errors or material inconsistencies. These defects can impact the aesthetic quality and may not meet the required standards.
- Assembly Errors: Defects can result from missing, incorrectly assembled, or improperly secured parts. Assembly errors often lead to non-functional products or those prone to early failure.
- Contamination: Foreign objects or substances can contaminate products during the manufacturing process, particularly in sensitive industries like food processing or pharmaceuticals. Contamination poses serious safety risks and can result in costly recalls.
Benefits of Implementing Error Proofing AI in Manufacturing
Using computer vision for error-proofing in manufacturing offers a range of advantages. Let’s take a closer look at how each of these advantages makes manufacturing processes better.
Increased Accuracy
One of computer vision's greatest perks is its ability to spot defects with incredible accuracy. These systems can detect the tiniest flaws in products, reducing the risk of missing errors or flagging non-existent ones. Also, by analyzing visual data over time, these systems can learn from past mistakes and further improve the accuracy of spotting defects. Human feedback is key here to retrain or fine-tune computer vision models.
Scalability
Computer vision systems are highly scalable, meaning they can easily adapt to different production lines and facilities. As manufacturing needs grow, these systems can expand without requiring major investments. They can smoothly integrate with existing processes, and manufacturers can improve their operations without needing to completely overhaul their setup.
Another interesting advantage is that computer vision systems aren’t limited to spotting defects. With the right infrastructure setup, a computer vision system can also be extended to tasks like inventory management and equipment monitoring. If a camera collects visual data and the images or videos are relevant, then multiple use cases could potentially be implemented.
Cost Efficiency
Automating visual inspections with computer vision not only reduces scrap and rework by detecting defects early but also cuts down on manual labor. Reducing human efforts lessens expenses related to hiring and training and minimizes the risk of human error. AI systems can process and analyze data at a speed unmatched by human capabilities. Beyond this, such systems can actually increase overall productivity and lead to quicker production cycles and better resource allocation.
Sustainability
The benefits of computer vision in manufacturing are more meaningful than just cost savings. Computer vision in error-proofing supports sustainable manufacturing by reducing waste and optimizing the use of resources. With better accuracy in defect detection, fewer products are wasted, and materials are used more efficiently. These computer vision systems can align with a company’s sustainability goals and reduce its environmental impact while promoting long-term success through continuous improvement and innovation.
Error-Proofing AI Challenges and Considerations
While computer vision brings many benefits to error-proofing in manufacturing, there are challenges and considerations to keep in mind to make sure that everything runs smoothly.
For example, setting up computer vision systems requires significant investment in high-quality cameras, sensors, and software. Often, existing equipment also needs to be upgraded to support these new technologies. While the long-term benefits are clear, the initial expense can be a barrier - especially for smaller businesses.
Other than this, computer vision models require high-quality data for model training. Sometimes, despite training models on high quality, variations in lighting, angle, or material can make consistent, accurate detections challenging. Developing algorithms that can handle such variability involves multiple rounds of testing and refinement.
Future Trends in Computer Vision for Manufacturing
The future of computer vision in manufacturing will likely involve paving the way for real-time processing and moving the industry closer to the goal of zero-defect manufacturing. Edge computing can be helpful for making real-time decisions in manufacturing. Instead of sending data to distant servers, edge computing makes it possible for manufacturers to analyze information right on the production floor. It reduces delays, boosts efficiency, and enables immediate responses to quality issues.
It also reduces the amount of data that needs to be sent over the Internet, saving bandwidth and costs while making the system more reliable. Processing data on the edge brings us closer to the concept of zero-defect manufacturing. Zero-defect manufacturing aims to completely eliminate defects and achieve flawless production by continuously improving processes and implementing error-proofing techniques.
Error-Proofing in AI Conclusion
By automating defect detection and reducing the need for manual inspections, computer vision helps manufacturers catch errors early, cut down on rework costs, and maintain consistent quality. With the added capabilities of edge computing and IoT, real-time processing and the goal of zero-defect manufacturing are becoming more attainable.
As the manufacturing industry continues to evolve, adopting computer vision can help you stay competitive. AI boosts operational efficiency and ensures that products meet the highest quality standards, leading to happier customers and greater business success. Now is the perfect time for manufacturers to invest in computer vision and build a stronger future in the industry!
Keep Reading
- An article on Bottle Cap Inspection with Computer Vision
- An article on Implementing Quantity Inspection with Computer Vision
- An article on How to Detect Metal Defects with Computer Vision
Cite this Post
Use the following entry to cite this post in your research:
Contributing Writer. (Aug 21, 2024). Error Proofing AI in Manufacturing. Roboflow Blog: https://blog.roboflow.com/error-proofing-manufacturing-computer-vision/